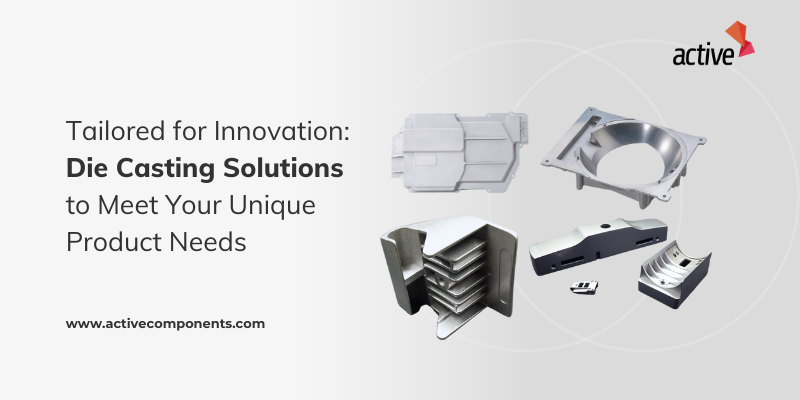
Why Choose Die Casting for Your Product?
In today's fast-moving product development landscape, precision, speed, and customisation are critical. At Active Components, we understand that the key to unlocking your product's full potential lies in the quality of the components and flexible custom solutions to meet your specific needs and challenges.
In this blog post, we'll delve into one of the most widely used techniques in product production - die casting.
What is die casting?
Die casting is a manufacturing technique used to produce metal components with a high level of precision and consistency. In this process, molten metal is injected under pressure into a mold, which is designed to shape the metal into a specific form.
This method is widely utilized across various industries to create a diverse range of products, including automotive parts, electronic components, and household appliances, due to its efficiency in mass production and ability to produce parts with complex shapes and fine details.
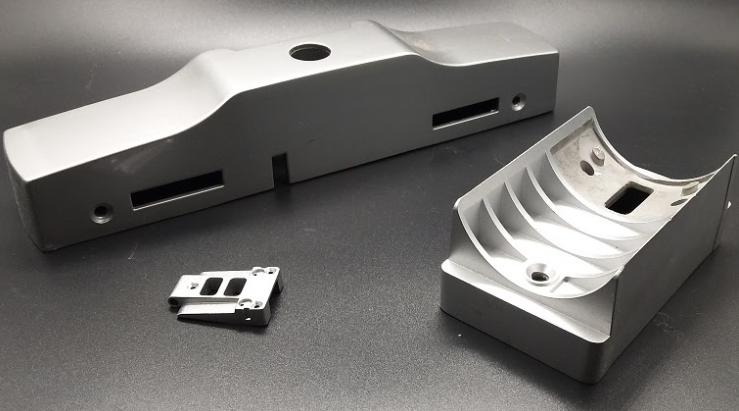
Types of die casting
Die casting is a versatile manufacturing process, differentiated into various methods, each offering distinct advantages. The two primary types of die casting are cold chamber and hot chamber die casting.
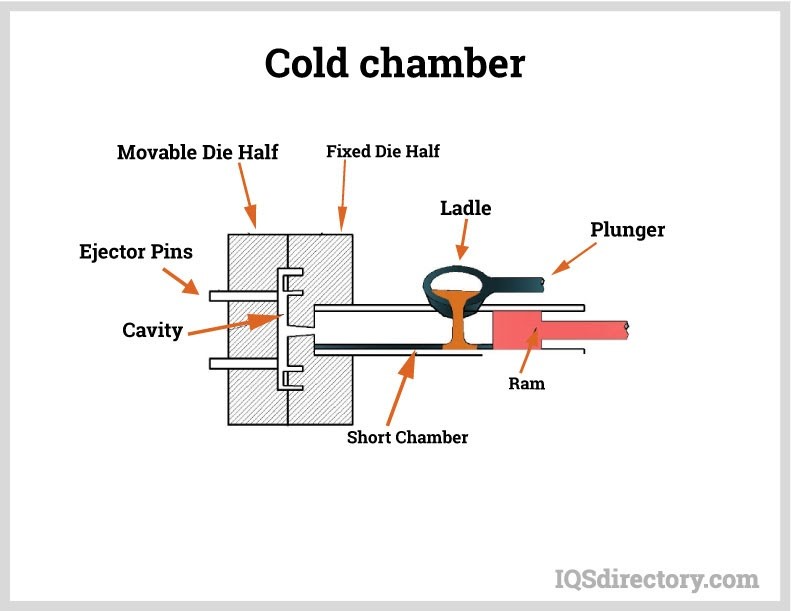
[Copyright: IQSdirectoyr.com]
Cold chamber die casting is used for metals with high melting points, such as aluminum, brass, and copper. In this process, the molten metal is manually or mechanically ladled into the injection system, keeping the injection machinery separate from the melting furnace. This method is preferred for metals that can chemically damage the pumping system over time, offering a solution for creating strong, heat-resistant parts.
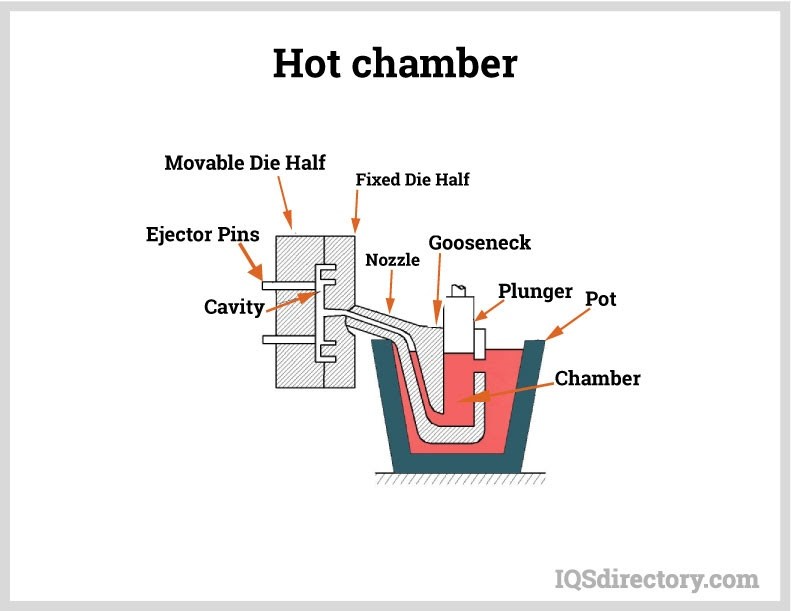
[Copyright: IQSdirectoyr.com]
Hot chamber die casting, on the other hand, is suitable for metals with lower melting points, including zinc, magnesium, and lead alloys. This process involves the injection machinery being submerged in the molten metal bath, allowing for faster and more efficient cycling times due to the close proximity of the metal supply. This method is ideal for producing small to medium-sized parts with good detail, thin walls, and high dimensional accuracy in a cost-effective manner.
Why Choose Die Casting for Your Product?
- Capability for Complex Designs: Die casting enables the creation of intricate shapes with precise tolerances.
- High Production Rate: Die casting is a quick process, beneficial for projects with tight deadlines.
- Reliable Repeatability: It allows for a high degree of repeatability, meaning that parts can be manufactured to precise specifications.
- Versatility Across Materials: Suitable for a wide range of metals, including aluminum, zinc, and magnesium, offering flexibility in material selection.
How can Active Components assist in this process?
Consultation Services: In a detailed consultation process, we provide expert recommendations based on our extensive experience in the product development process. This involves continuous refining and sourcing parts including electronic components and complex metal parts to perfectly align with the engineer’s requirements.
Collaboration with Manufacturers: A manufacturing partner must understand the part’s application, desired materials, and timeline. With over 40 years of experience, Active Component has established robust relationships with premier manufacturers of electronic components worldwide. By working closely with accredited and trustworthy manufacturers, we produce dimensionally accurate precision parts with a high-quality finish.
Inventory Management and Stock Availability: We provide inventory management services from our warehouses, with options to hold stock in New Zealand and Hong Kong. This ensures that our customers can quickly respond to spikes in demand or plan against demand forecasts.
Through our partnerships with leading manufacturers, Active Components provides solutions like die casting services that bring unparalleled precision, speed, and adaptability to your product. This approach ensures that your product is crafted to stand out in a competitive market.